A Turner’s cube is a classic machinist’s exercise that challenges the skills of someone who turns on a lathe.
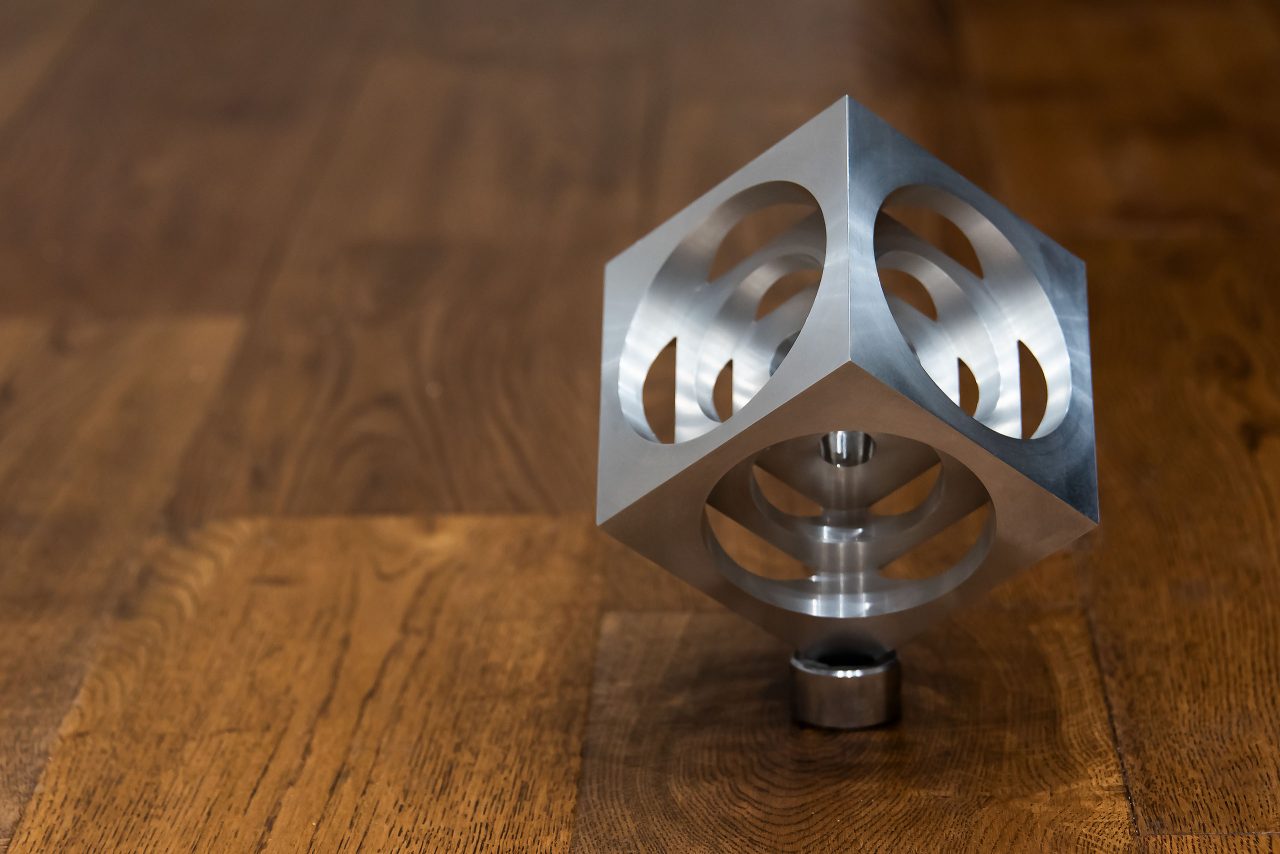
This was the first project on my new lathe – because I hadn’t heard of it before, and it looked cool! I designed it in 3D first using Design Spark Mechanical (see my 3D Modelling page), which is freeware. You will note that the 3D model has 4 cubes, but I chose to go with 3 in the end.
I chose to build a large one to test the capability of the lathe to hold and machine large chunks of metal. So I started with a 100mm3 aluminium block.
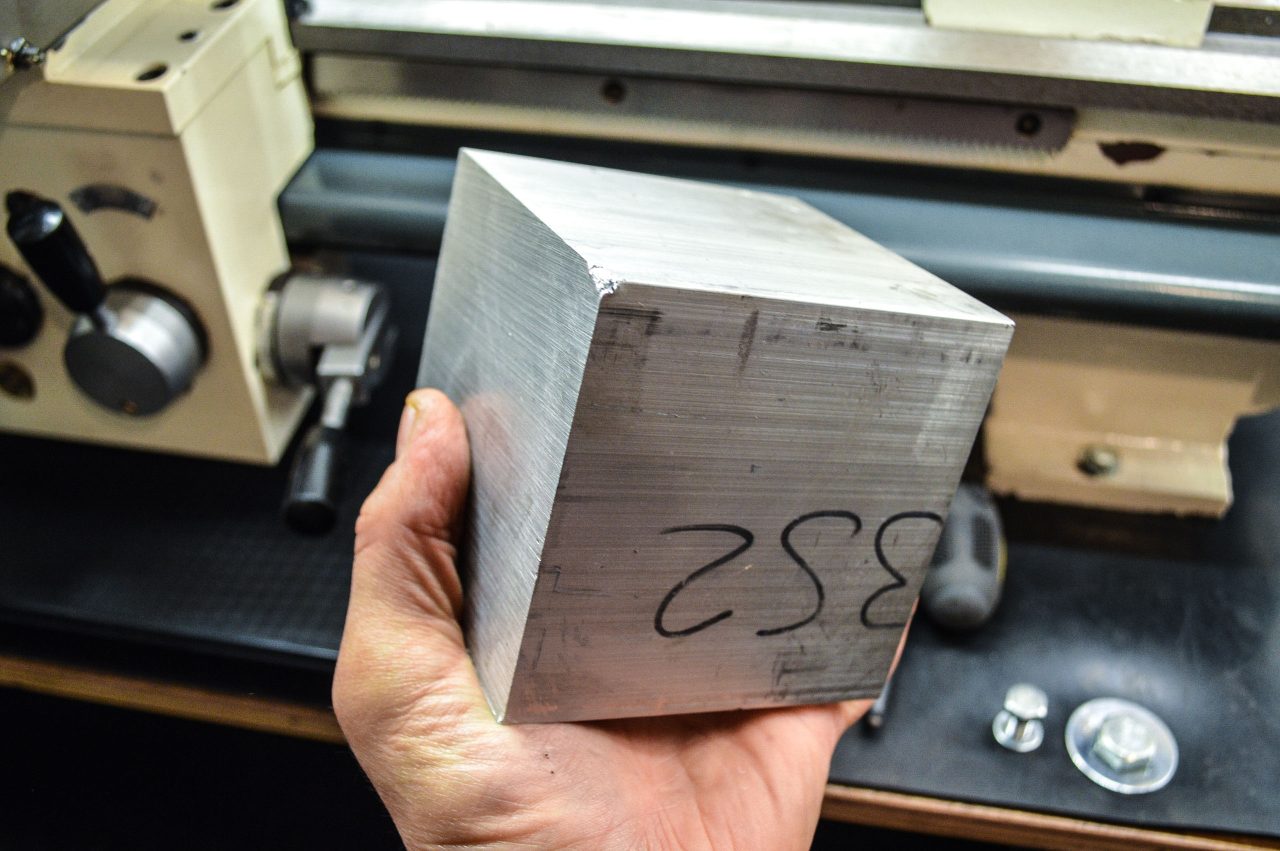
This fitted nicely into the 4 jaw independent chuck.
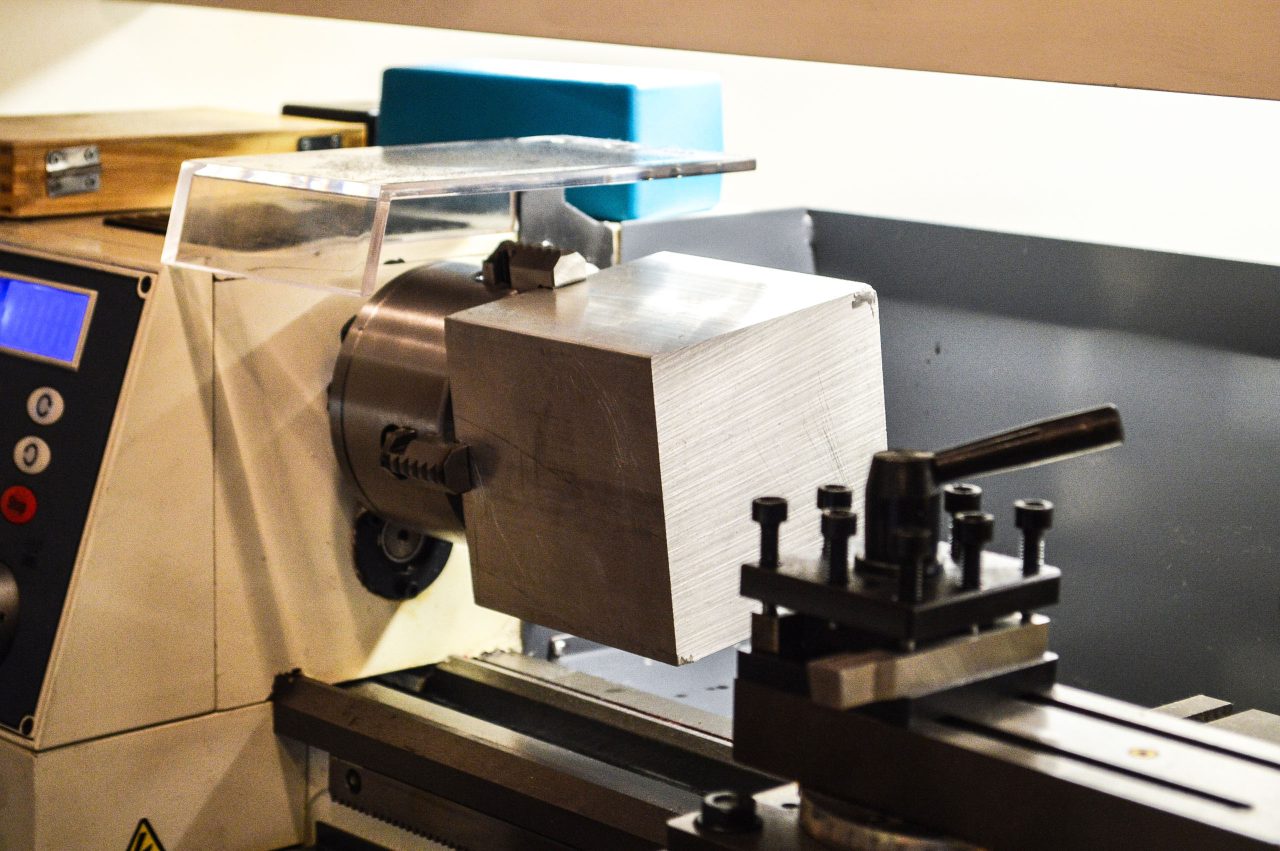
The first task was to face one side of the cube to create a reference surface.
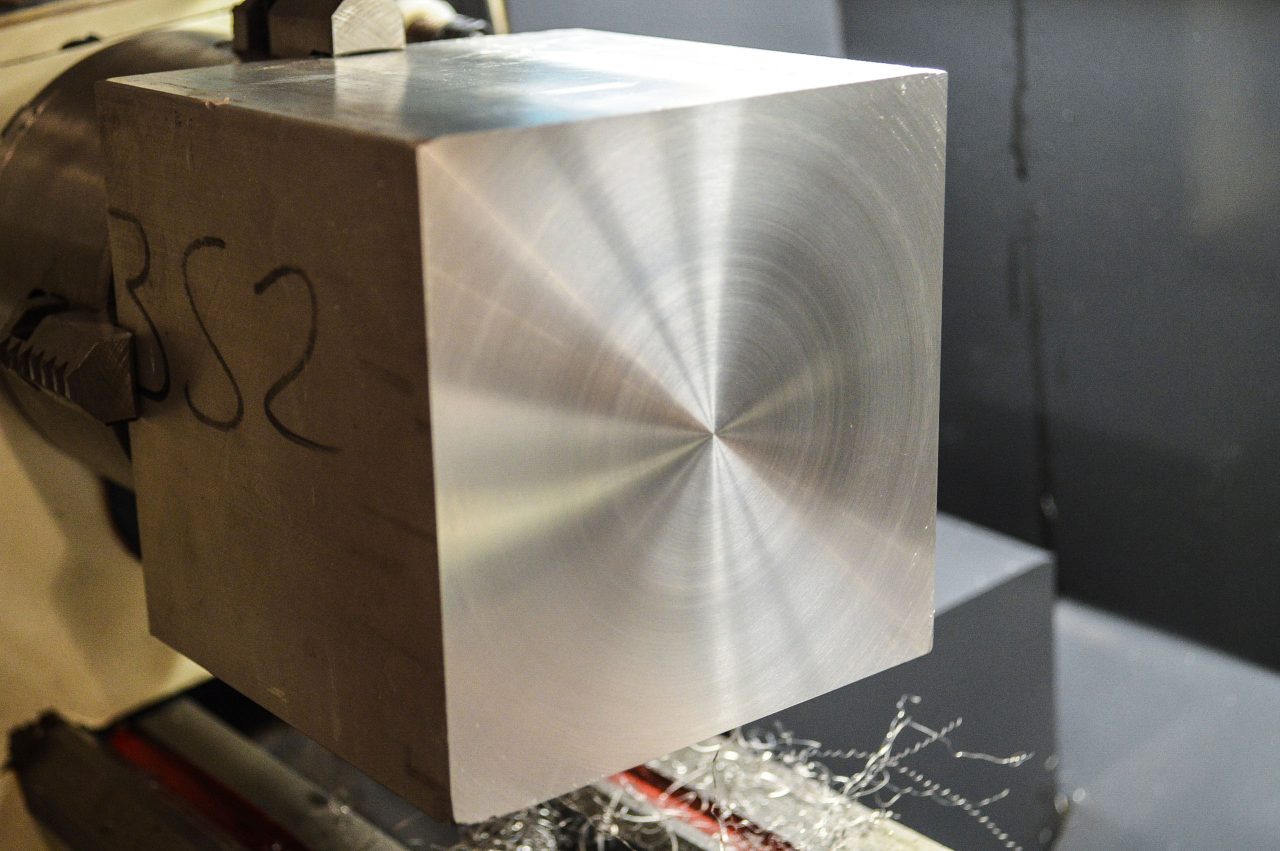
I started cutting the circular recesses into the sides, rotating and realigning the cube in the 4 jaw chuck for each cut. In hindsight, it would probably have been better if I made all the cuts and drilled the holes in each side before rotating the cube, as I spent a lot of time realigning it. To align the cube in the chuck I had to adjust one jaw at a time and use a dial test indicator to ensure that it was centred.
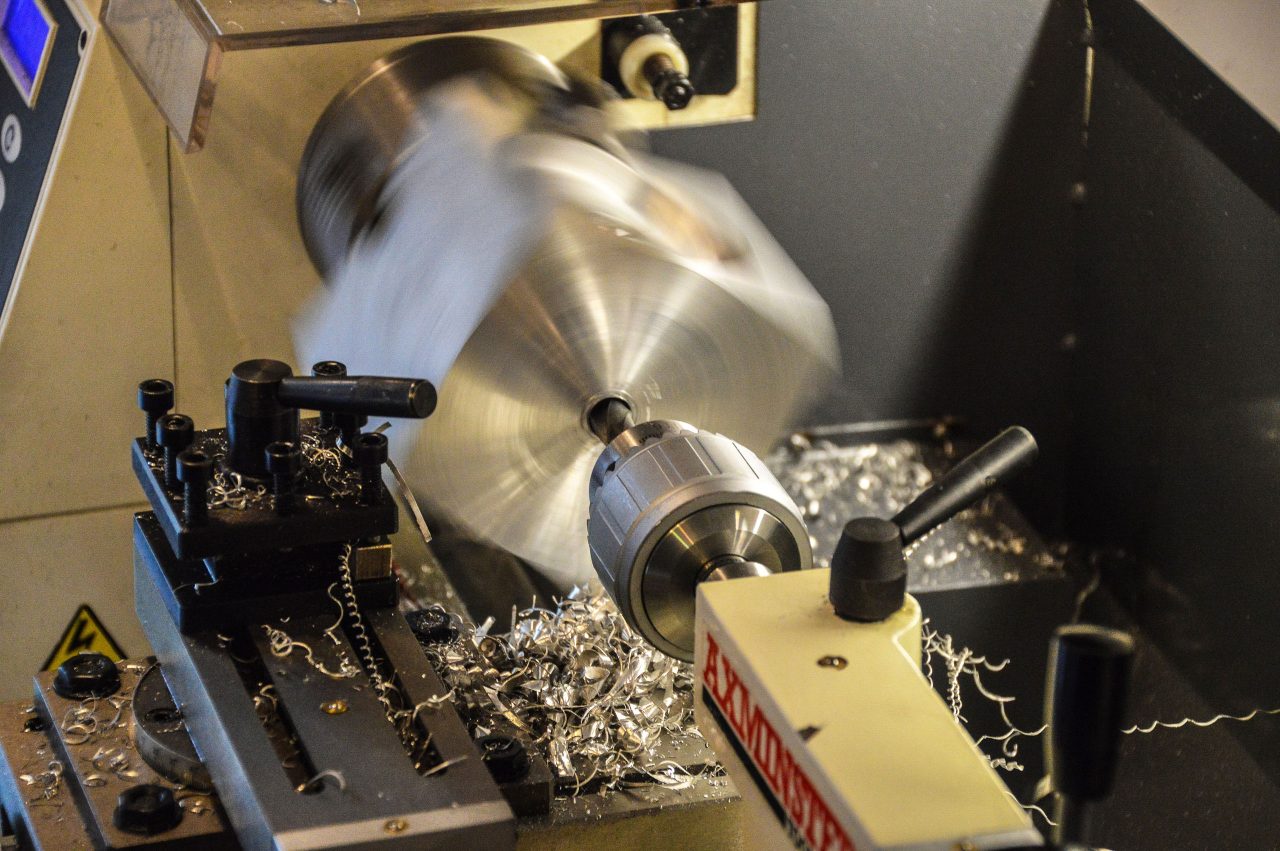
A lot of material had to be removed and a loads of swarf generated!
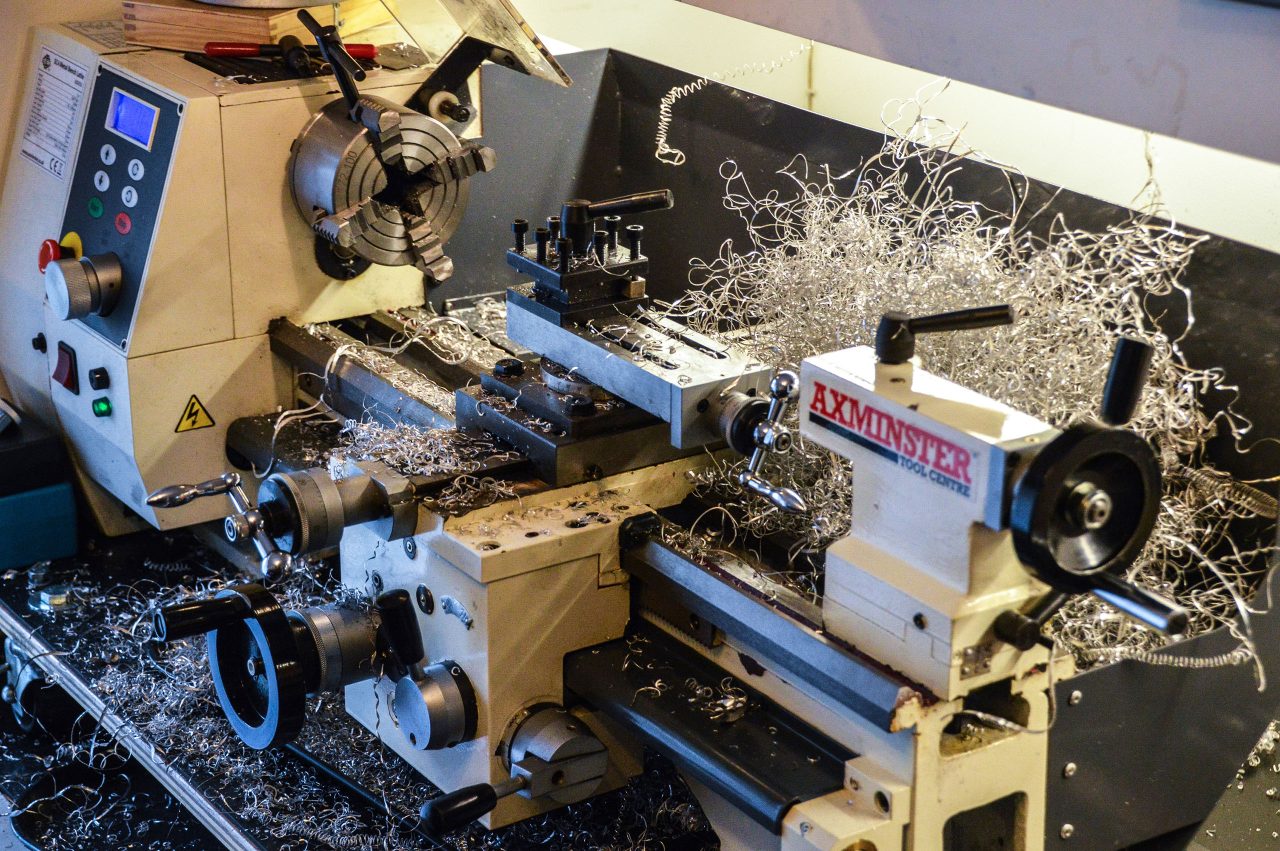
The partially finished Turner’s cube.
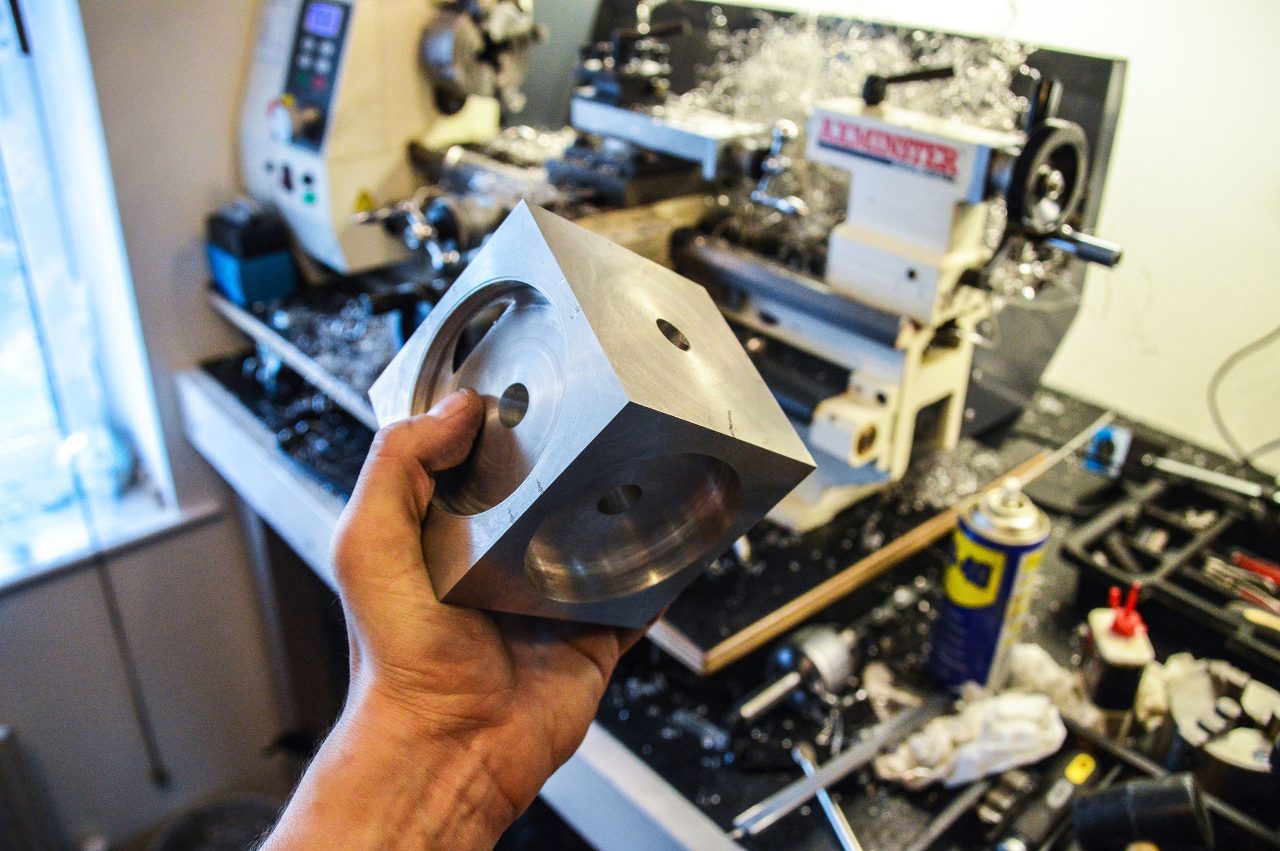
All first level cuts completed.
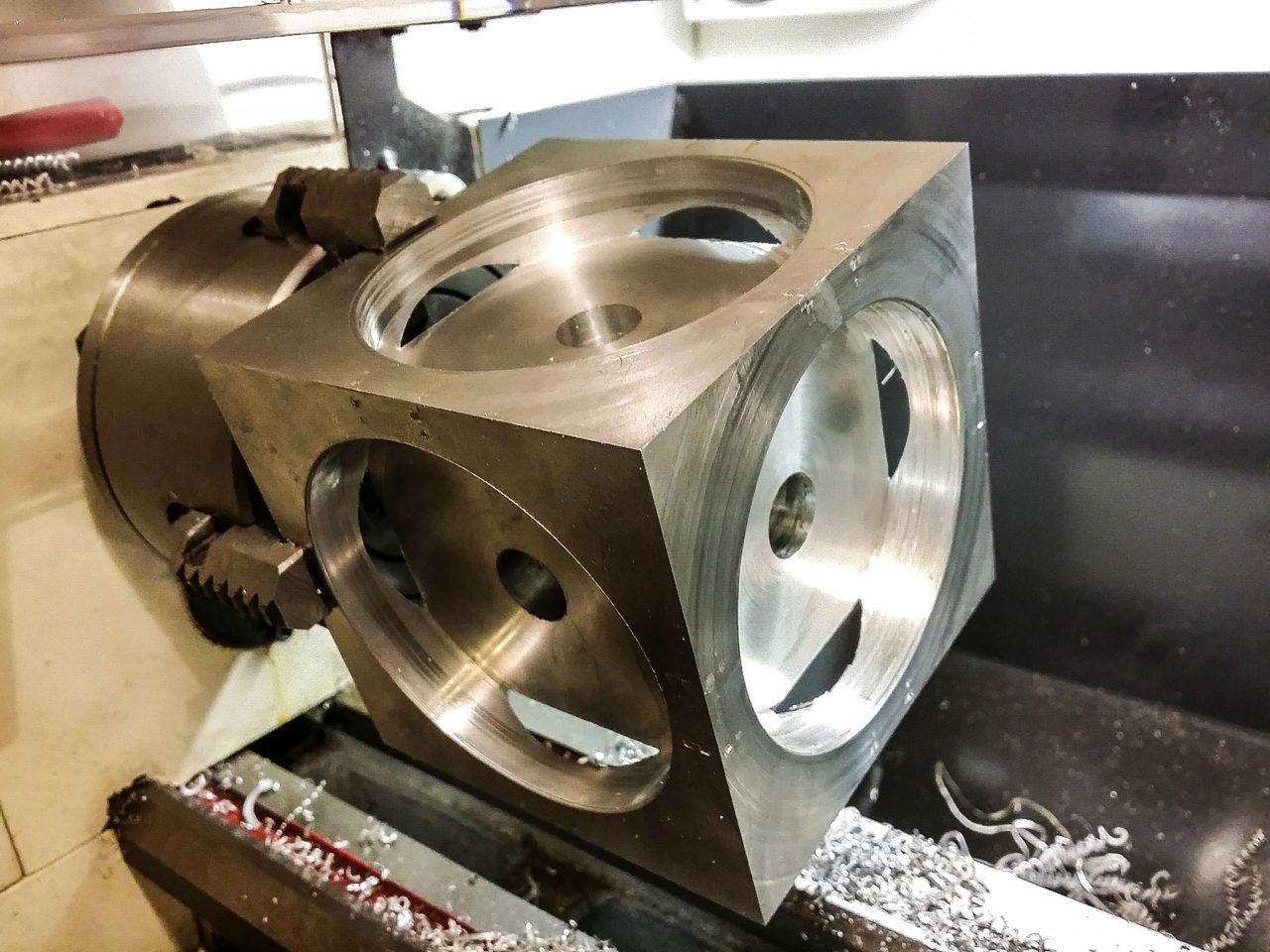
This is a video I put together showing the lathe in action. Here we are facing the cube, drilling and cutting the recessed circles.
The finished product.
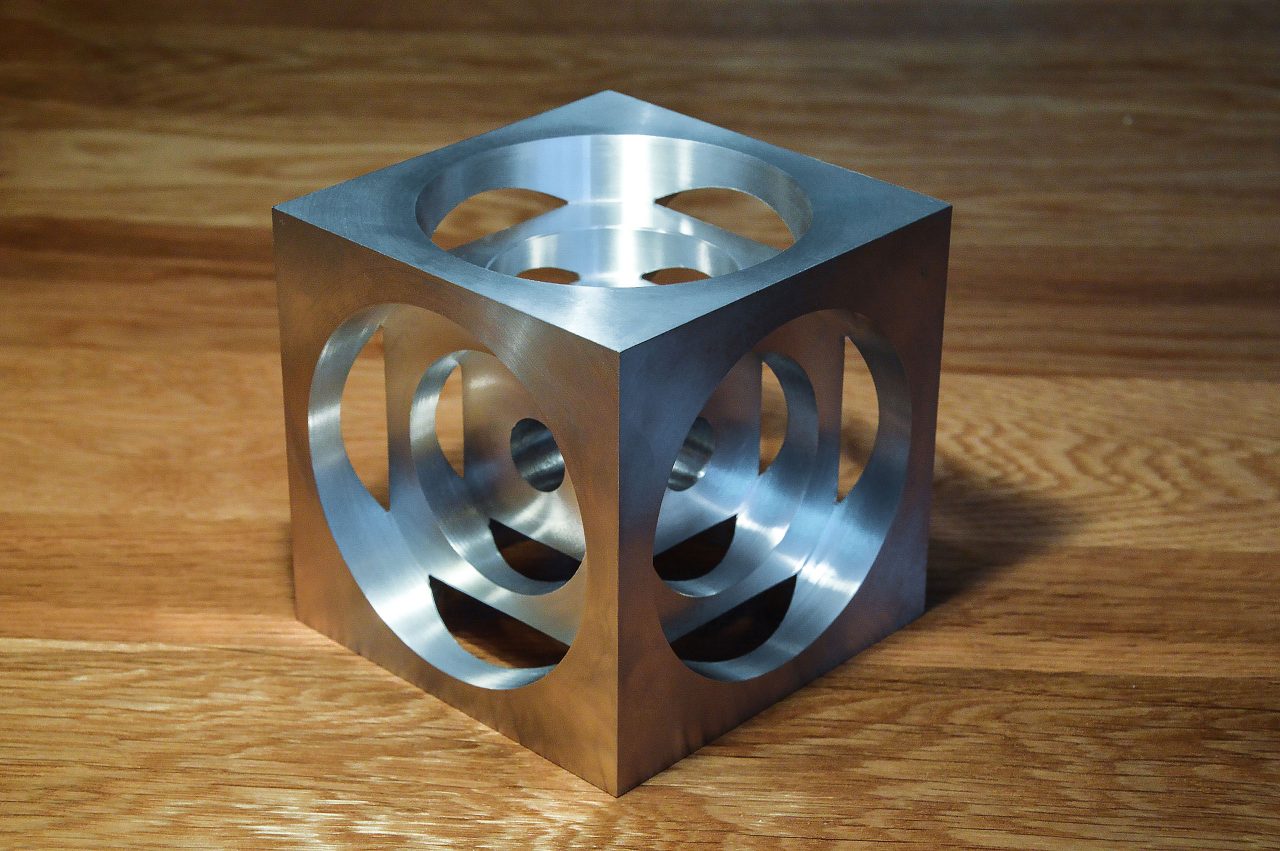
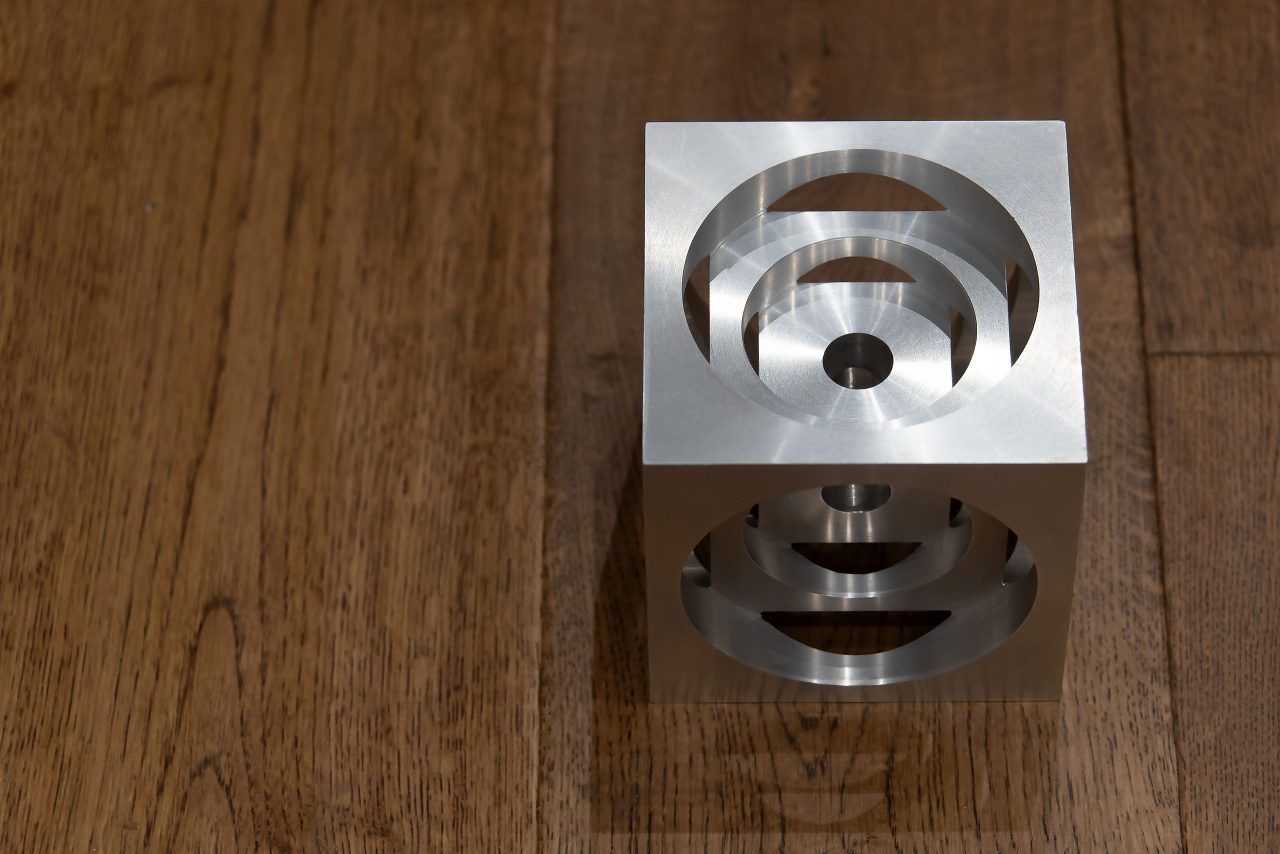

Leave a Reply